Get In Touch
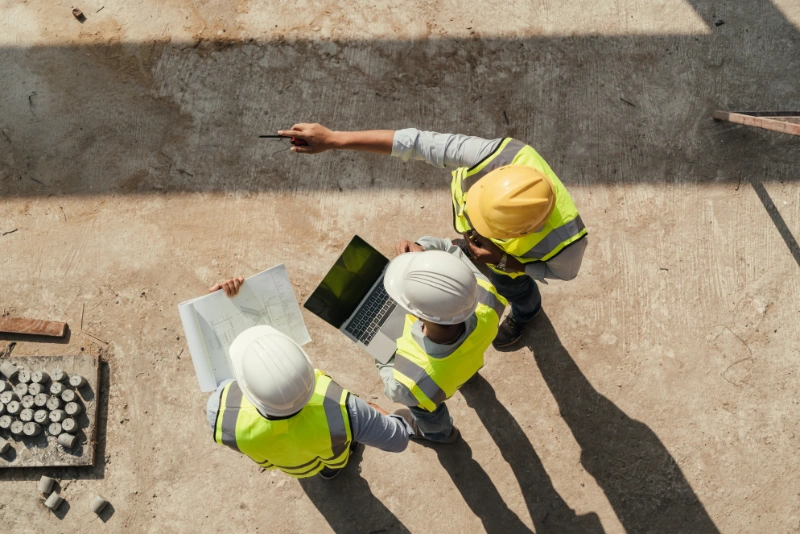
Get a Quote
Common Questions
How accurate are your GPS models?
Our GPS modeling and machine control models are meticulously crafted to ensure GPS-guided equipment operates with precision on the job site. We focus on every detail, from grading information to terrain features, ensuring each model is perfectly aligned with the site’s specific requirements. Comprehensive quality checks are conducted to verify accuracy and reliability before delivery.
What information do you need from us to get started?
To begin, we will need the site plans, grading information, and any relevant engineering drawings. The more detailed the plans, the more precise the model or takeoff will be. Sharing AutoCAD files is also highly beneficial. If there are any specific requirements or complexities associated with the project, please make sure to include those details as well.
How long does it take to complete a machine control model or material takeoff?
The timeline varies based on the project’s complexity and size. For simpler models, it may take just a couple of days, whereas more intricate projects could take up to a week. We will outline a specific timeline in our proposal after evaluating the project’s requirements.
Can you handle revisions if the engineer’s plans change?
We completely understand that changes can occur, and we are prepared to revise the models or takeoffs as necessary. Depending on the scale of the changes, we may need to modify the timeline or costs, but we will always communicate any adjustments clearly in advance.
What if the grading information provided is incomplete or unclear?
If the grading information is incomplete or unclear, we can use our expertise to interpret the design intent. However, this may lead to increased time and costs, as we must ensure that the final model accurately meets the project’s requirements.
Do you offer on-site support to ensure the model works correctly with our equipment?
Yes, we plan to offer on-site support as part of our service expansion. This will include setting up GPS base stations, localizing the model to the site, and providing technical assistance to ensure everything functions smoothly with your equipment.
How do you price your services?
Our pricing is based on the complexity and scope of the project. For machine control models, factors such as the number of building pads, detailed features like curbs or sidewalks, and the quality of the provided grading information all play a role in determining the cost. Material takeoff pricing is based on the amount of detail required and the size of the project. We always aim to provide a fair and transparent quote in our proposal.
Do you offer discounts for multiple projects or long-term contracts?
Yes, we can discuss discounts for clients who have multiple projects or are interested in establishing a long-term partnership. We value ongoing relationships and are happy to tailor our pricing to reflect that commitment.
What if there are issues with the model once we start using it on-site?
We stand by the quality of our work and provide support if any issues arise during the use of our models. If there are discrepancies or adjustments needed, we’ll work with you to resolve them quickly to keep your project on track.
How do you ensure that your material takeoffs are accurate?
Our material takeoffs are meticulously calculated using the latest software and industry best practices. We cross-check quantities against project specifications and plans to ensure accuracy. Additionally, we provide detailed reports so you can review and confirm the numbers before moving forward.